In the food and beverage industry dairy, abattoirs and meat processors, bottled beverages, breweries, baked products, and flour and cereal facilities there is a high demand for hygiene and water treatment in order to maintain high quality end product standards and prolong shelf life. Industrial food and beverage facilities test impurities in their production water and verify the efficiency of solutions to ensure that all process water consumed remains suitable for use in their production processes.
With growing international and local pressure, the food and beverage industry has to look for new ways of steering its product development and achieving continual control over costs and health risks in a bid to meet the demands of its customers. As such, water is a major issue, whether it is an integral part of production processes, involved in product composition, or used for refrigeration, steam production or cleaning operations. To keep water consumption under control and ensure the reliable operation of its production, while taking account of seasonal variations and new product lines, industries are looking for a safe and top-quality water supply.
Iron is an essential micro-nutrient in soils, however iron dissolved in industrial irrigation water can cause problems when it precipitates. Iron and Manganese present a wide range of problems in many industrial applications that use untreated water including:
- Clogging of irrigation lines
- Clogging of nozzles
- Staining
- After taste in food treatment
- Non compliance with health standards
Beverage manufacturers and processors face unique challenges in the area of water treatment. Water sources, disinfection processes and treatment residuals can affect the taste and quality of the final product. Beer and soft drink production starts with a pure source of water. Drinking water often includes trace amounts of various ions that alter its taste. Contamination of beverage drink process water can result in loss of product (not only resulting in production losses, but also higher waste effluent surcharge costs), product recalls, and lost consumer confidence. Bottlers use filtering and other treatment equipment to remove residual impurities and standardize the water used to make drinks.
Fresh products facilities face significant financial losses due to decay as fresh produce from producer to consumer. Bio fouling from excess Iron and Manganese will stunt the growth of fresh produce and inhibit the supply of consumer crops to market.
In dairy, abattoirs and meat processors all water used must be compliant with the relevant guideline. From slaughtering to cleaning to processing – water source, process water and waste water has to be free from iron and manganese. Iron and Manganese contamination process water will infuse into product, create boiler issues and clog pipes and sprinklers.
Many of these problems adversely affect the underlying performance of the water reticulation systems in use, resulting in lost productivity, or the need to over invest in capital equipment.
DMI-65 is an extremely powerful silica sand based catalytic action water filtration media that is designed for the removal of Iron and Manganese without the use of potassium permanganate through an Advanced Oxidation Process. It also performs a mechanical filtration function for the removal of solids from the water.
Incorporation of DMI-65 in water treatment systems will materially reduce these symptoms and allow the reticulation systems to perform to their designated levels.
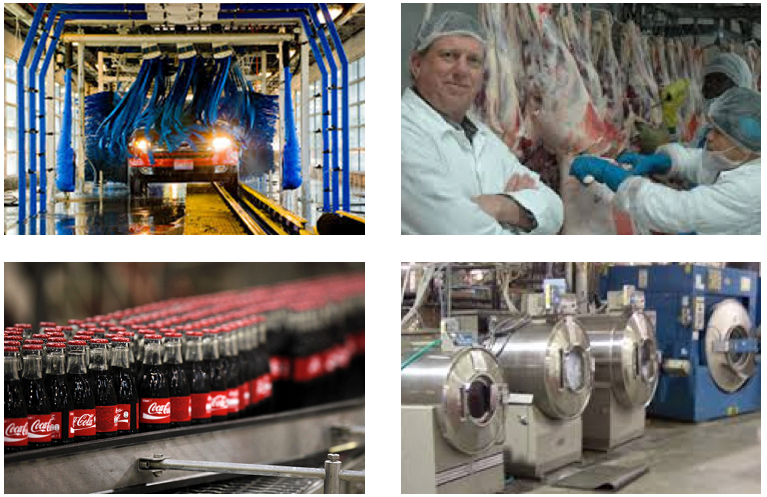
DMI-65 is used in a wide variety of food and beverage applications
DMI-65 is infused technology and not just a surface coating technology, unlike other catalytic water filtration media, which removes the chance of any chemical leaching into the water stream.
In order to begin the process of oxidation of the iron (and manganese) in solution DMI-65 is designed to operate in the presence of chlorine or other oxidant. In this process the oxidant removes electrons and is consumed in the process. The operator needs to ensure that there is a 0.1 – 0.3 ppm free chlorine residual in the effluent water. Chlorine, fed as sodium hypochlorite or bleach (12.5% NaOCl), is the preferred oxidant since it is relatively inexpensive, readily available around the world and it is effective. It also performs the vast majority of any disinfectant process.
Unlike ion exchange resins where higher regenerant dosages will increase the ion exchange capacity, NaOCl residuals or concentrations higher than required to oxidize the Fe and Mn do not increase the oxidative properties of the media. Additionally, since the media is often used to pretreat waters prior to an RO system a higher free chlorine residual would require more extensive post treatment to reduce the residual and protect the membranes from chlorine attack.
DMI-65 has been certified to the US Standard of NSF/ANSI 61 for Drinking Water System Components and for use in England and Wales Under Regulation 31(4)(a) of the water supply (Water Quality) regulations 2010 and has also been tested by many other water treatment authorities and laboratories.
Case Study.
A meat processing plant located in the Texas panhandle required a daily cleaning of the processing area. The water had 2 ppm of iron and 1.5 ppm of manganese resulting in frequent change-out of the cartridge filters on the water pump skids at a cost of $6000 per week. In addition to this expense the water did not meet the FDA guidelines for food plant wash-down water due to the presence of the iron and manganese. In 2011 768 ft3 of the DMI-65 was installed in a new 1500 gpm system comprised of sixteen (16) 54’ x 60” filter vessels. Since the system was placed into operation the cartridge filter replacement went from weekly to semi-annually and the iron and manganese in the wash-down water is now within limits.
Advantages of using DMI-65: Water Treatment Food and Beverage
Regulatory Compliance. DMI-65 efficiently removes dissolved iron to the almost undetectable levels as low as 0.005 PPM and manganese to 0.001 PPM which will allow the use of treated water in the highly regulated food and beverage industry.
Reduced Costs The total cost of the iron and manganese removal water filtration system is significantly less than alternative solutions, the effectiveness, but relative simplicity, of DMI-65 based systems reduces the upfront capital expenditure on plant complexity as well as the ongoing operational expenditure in chemicals, power and backwash waste water recovery.
High Flow Rates. The infused technology of DMI-65 promotes the highest oxidation rate of any catalytic filtration media. This permits a significantly higher water flow rate to achieve the same level of iron and manganese removal. DMI-65 can operate at linear filtration velocities up to twice that of conventional media with a corresponding reduction in capital equipment costs.
High Load Capacity Because of the increased surface area due to the micro porous structure of the matrix material, DMI-65 also has higher iron and manganese load capacity which can extend the duration of filter runs and the time between backwashing, thereby reducing downtime, operating expense and wastage.
Regeneration Not Required. The media operates with a continuous injection of sodium hypochlorite at low residual levels (0.1 to 0.3 ppm) which eliminates the need for Potassium Permanganate.
Wide Operating Environment. Stable and satisfactory performance at pH 5.8 to 8.6 and a maximum operating temperature of 113° F (45°C) reduces the need for investment to alter the operating environment.
Long Life. DMI-65 is not consumed in the process giving it an expected operational life of up to 10 years, providing considerable advantages over other processes or media. The media does not display a decaying capacity to do its catalytic work. Over the 5 to 10 year period, through many backwashing operations of the bed to remove retained solids, an attrition loss of the media occurs by contact between particles and mechanical abrasion